The Objective
Our team worked in collaboration with a third-party Fuel Systems Contractor to provide the following site works:
- Ventilate the tanks utilising venturi system to ensure safe access
- Complete a comprehensive structural integrity and condition assessment of the tanks
- Complete a clean and abrasion of all tank internals
- Remove any damaged or delaminating existing fibreglass
- Repair any cracks and imperfections in the existing tank
- Install the 6mm FRP structural lining
- Maintain safe access for fuel tanker deliveries
The Challenge
At TRL’s Viva Norwest project, we encountered several challenges that required strategic planning and effective problem solving. This included:
- Fuel tanker fill point within close proximity of working zones
In order to continue fuel product sales, multiple fuel tanker deliveries were required within our enclosed site area. - Tank assessment and repairs
To determine the validity of tank lining works a comprehensive structural integrity and condition assessment and subsequent repair methodology was required to be submitted to the client prior to commencing works. - Safely operating within a very busy site
A particularly complex obstacle was the need to safely continue our works within a bustling public space, with the surrounding service station, carwash, bottle shop, shopping centre, and main road.
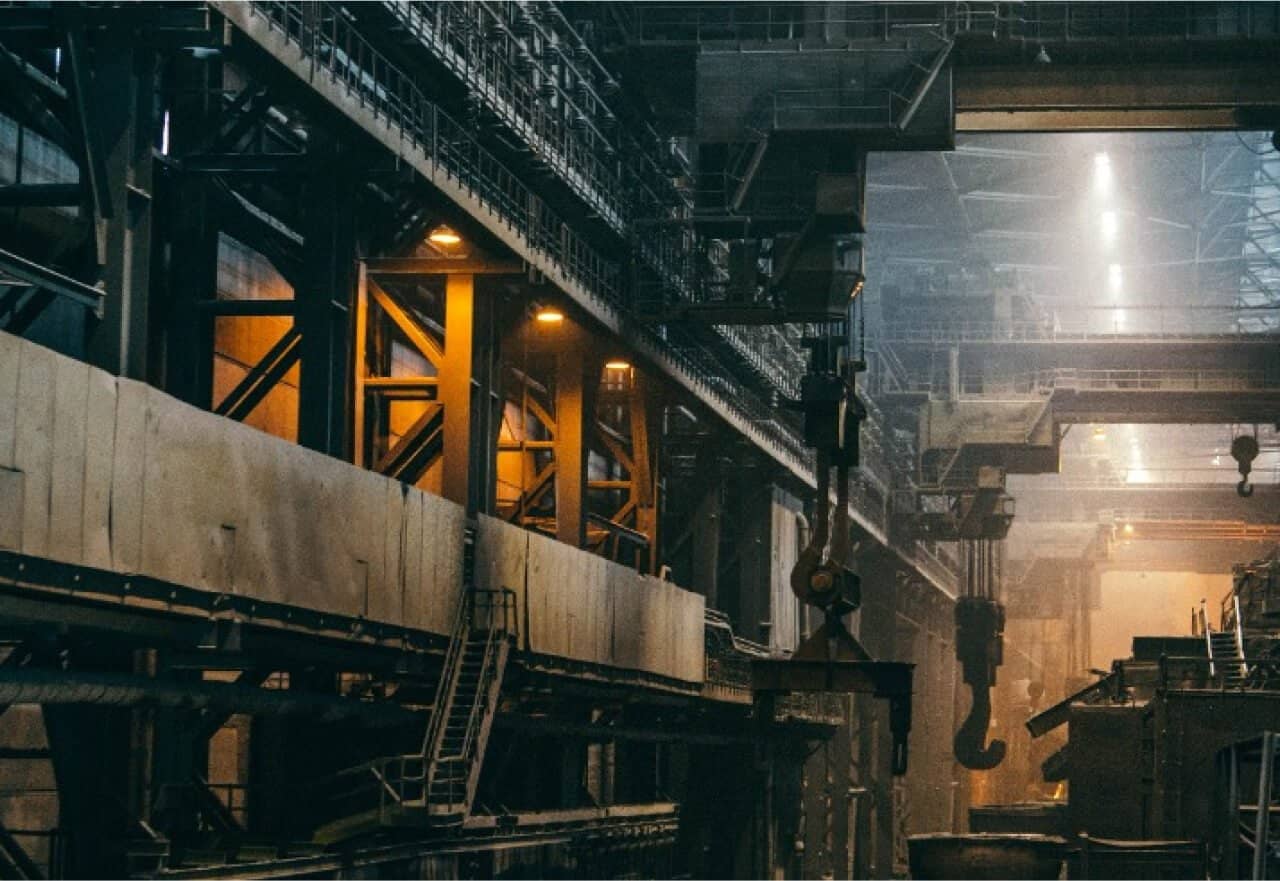
The Solution
We achieved the successful completion of the Norwest project by diligently adhering to a set of crucial objectives:
- Despite fuel tanker fill point within close proximity of working zones, TRL were able to effectively stage the timing of fuel deliveries and simultaneously coordinate site equipment pack down and setup during these times. Effective communication and continuous planning with the client and fuel systems contractor was imperative to minimise any delays and eliminate variations to the project.
- Tank assessment and repairs were immediately conducted after safe access was made to the tank. The assessment and subsequent repair methodology was supplied within 24 hours of entering the tank which eliminated any delays to the project timeline.
- Undeterred by operating within a very busy site, TRL developed and implemented a comprehensive safety protocol to ensure the secure operation of equipment and personnel within a highly congested and bustling work site, with a focus on minimizing risks, optimizing communication, and maintaining efficient workflow.
Takeaways
- Project Delivery
TRL ensured that each stage of the project was delivered on time, with effective communication to all stakeholders provided throughout the duration. - Maintain Site Product Sales
Through proactive planning and communication a minimum of 3 fuel products were available to the public during the duration of the project. - Safety
TRL performed all works in accordance with established Safe Work Procedures and a specific WHS&R Plan. Our team have up to date confined-space rescue and first-aid training, and were also working alongside an OHS Officer. - Minimising Risk
Our Fibreglass technicians and Engineering team at Norwest were comprehensively trained in Confined-Space Entry and Rescue, Gas Testing, Operation of a Breathing Apparatus, Working at Heights and WPCG Accredited. - Environmental responsibility
Reduce, Reuse, Recycle. Compared with replacing tanks, TRL’s FRP lining systems significantly reduces the amount of excavation and materials required. Instead of discarding an entire old tank, TRL’s FRP lining process reuses it as the formwork for a brand-new standalone tank flow.
Conclusion
The Viva Norwest project demonstrated TRL’s ability to conduct complex maintenance and lining activities within a live and busy operational site, emphasizing the importance of safety, planning, and efficient execution. The successful completion of this project ensures the continued safe and reliable operation of the USTs at the Viva Norwest site.