The Objective
- Ventilate the tanks utilising venturi system to ensure safe access
- Access the tanks with our tried and tested cold-cutting technique
- Complete a comprehensive clean and inspection of all tank internals
- Reinforce any cracks in the existing tank shell
- Install a Fibre Reinforced Plastic (FRP) manway to engineered specifications
- Install the Intanka© double walled structural lining
- Install an interstitial tank monitoring system
- Install two new transition fittings in accordance with the design specifications supplied by the Fuel Systems Contractor
- Install a new steel manway cover with six sockets
The Challenge
At TRL’s Ampol Woolooware project, we encountered several challenges that required strategic planning and effective problem solving. This included:
- Operating within the constraints of a very small site
A particularly complex obstacle was the need to maximize the operational capacity of the small but bustling service station, while conducting extensive construction work. - Securing the in-situ tanks despite hydrostatic pressure from high groundwater
TRL was tasked with assisting with ensuring the stability of the existing partially excavated empty tanks under threat from high groundwater conditions. - Supply chain disruptions
TRL faced disruptions in the supply chain, particularly due to material shortages, including a national shortage of 600 GSM fiberglass and Polyester Resin.
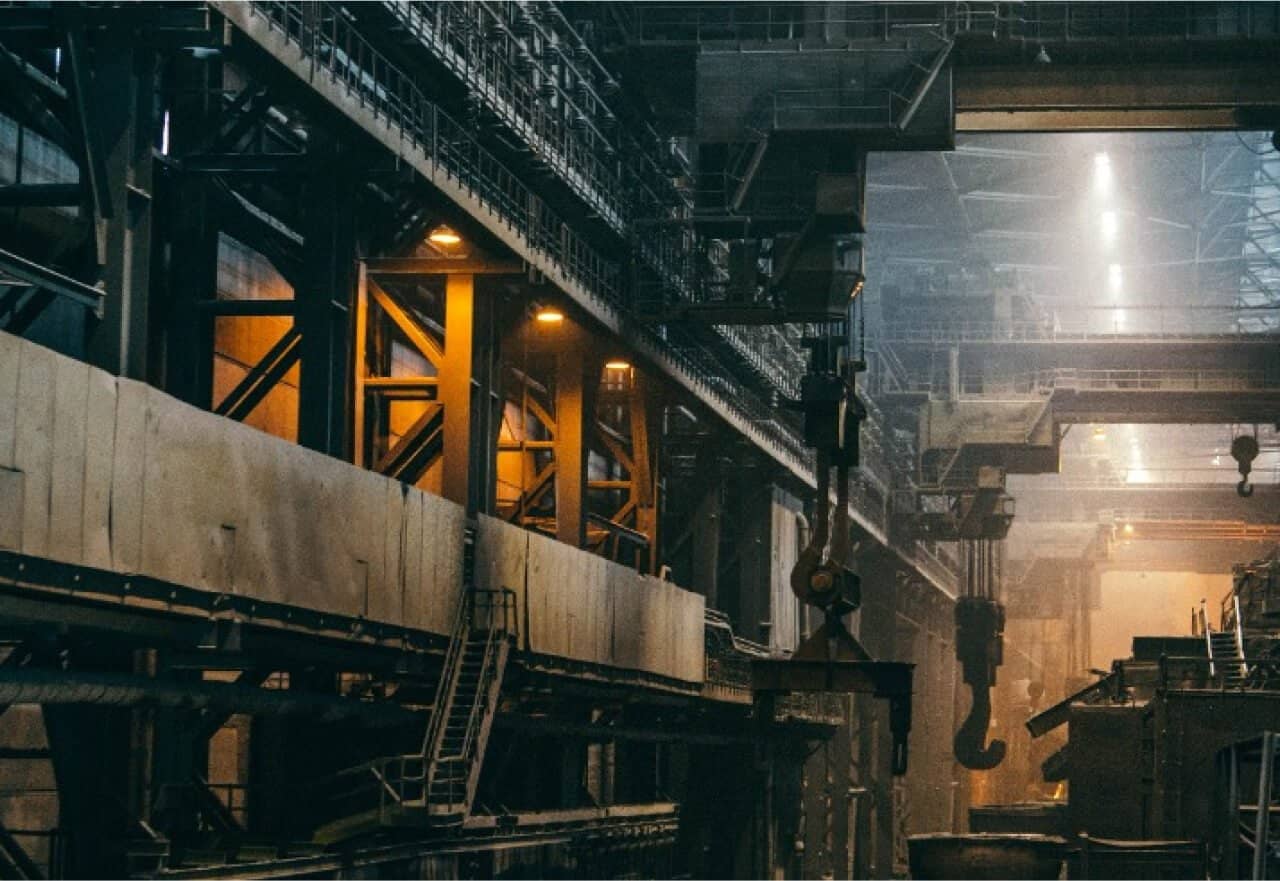
The Solution
- Despite operating within the constraints of a very small site, TRL were able to stage the layout and sequencing of the Intanka™ construction to maximise efficiency within the limited space. This required critical collaboration with the Fuel Systems Contractor to determine specific fuel requirements despite removing 75% of the storage tanks from service. The civil excavation works were completed in several phases to ensure safe entry and exit for vehicles accessing the fuel pumps.
- To secure the empty in-situ tanks at Ampol Woolooware TRL ensured that a partial excavation exposed only the necessary sections at the top of the tank that were required for the manway and transition fitting installations. A poured concrete anchoring system was also implemented proactively due to a weather forecast of heavy rain during the second stage of the project works.
- Supply chain disruptions were solved by diversifying suppliers of our fibreglass products, whilst not substituting for the quality materials we guarantee. Our project management team also engaged in proactive procurement planning with our supplier Allnex, to prevent an almost certain shortage of Polyester Resin.
Takeaways
The project at Woolooware was completed successfully by adhering to several key objectives:
- Project Delivery
TRL ensured that each stage of the project was delivered on time, with effective communication to all stakeholders provided throughout the duration - Quality assurance
All three tanks at Woolooware were built to specific quality production standards (including UL1316:2018), and have an independent engineering certification - Safety
TRL performed all works in accordance with established Safe Work Procedures and a specific WHS&R Plan. Our team have up to date first-aid training, and were also working alongside an OHS Officer. - Minimising Risk
Our Fibreglass technicians and Engineering team at Woolooware were comprehensively trained in Confined-Space Entry and Rescue, Gas Testing, Operation of a Breathing Apparatus, Working at Heights and WPCG Accredited. - Environmental responsibility
Reduce, Reuse, Recycle. Compared with replacing tanks, TRL’s Intanka™ reduces the amount of excavation and materials required. Instead of discarding an entire old tank, the Intanka™ process reuses it as the formwork for a brand-new tank.
Conclusion
Through careful planning and forming a close working relationship with the Fuel Systems Contractor TRL were able to effectively coordinate activities and address the challenges outlined above.